Tips On Performing Inventory Counts
The Hardest Part
All inventory counts are important, but the count we’re concerned with here is your initial count. Maybe you’re counting your stock levels for the first time, or perhaps you don’t trust your current numbers and want to start clean. Whatever the reason, if you’re going to get a complete count of your stock, this document will provide help and insight. If you already have a trusted picture of your current inventory levels and don’t feel the need to visit this subject, than you can certainly skip this section. If you’re using Clearly Inventory, this section will explain how to get the information you will need to load in the “current inventory” table.
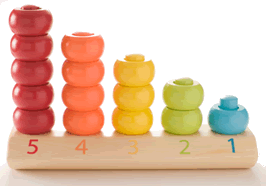
Tips on Performing Initial Inventory Counts of Your Entire Stock
Key Decisions to Make Before Conducting your Count
- Why are you counting your inventory?
- What are you going to count?
- Where are you going to count?
- When are you going to count?
- Who is going to be doing the counting?
Get right to the point below, or scroll down for a thorough explanation.
Why Are You Counting Your Inventory?
You probably already have a good reason for counting your inventory. But this is a good time to consider other benefits to keeping track of your inventory and the other reasons for tracking it. The following list of reasons is meant to remind you of common reasons for performing inventory counts as well as stimulate your imagination as you think about why you’re doing this.
Asset Tracking and Valuation
Most businesses have a large part of their capital tied up in assets. These assets may be things like buildings, automobiles, machinery, furniture, fixtures, equipment, and computers. Often businesses need to know the value of these assets along with other information as to where they are, when they were purchased, for how much, etc. This information may be needed by your accountant, banks, insurance companies, partners, people in operations, and management. You can’t get the best use of your assets if you only have a vague idea of what they are, where they are, and what they cost. This is as good a time as any to count your longer-term assets.
Managing Stock Levels
Can you save money while still delivering your products on time? Are you chronically overordering certain items? Do you need to free up space for other products? If these business decisions are important to you, then you will need to have a count of the items that may be involved.
Anticipating Demand
If you are in a business or enterprise that experiences demand changes based on the seasons, time of year, holidays, days of the week, etc., then you will want to have accurate inventory counts of those items that are most affected by these factors. You’ll want to know how much of an item you used last time and how much was left over so you can decide how much to buy this time.
Shrinkage, Theft, & Loss Control
If people know that no one’s keeping track of things, they will tend toward carelessness at best and outright theft at worst. When an organization demonstrates through actions that an accounting of its goods and equipment is a regular part of their operations, people will know that someone’s paying attention, and they had better do so as well.
Insurance
If disaster strikes, how quickly will you be able to account for all of your stock and equipment? And if you keep track of these things, where are those records kept? on site? When considering why you’re counting your stuff, ask yourself what you’d want to know if everything was gone tomorrow. What would your insurance company want to know?
Accounting
Do you need to provide your accountant with a value of your current inventory at the end of every fiscal year? Will you need to at some point in the future? A solid record of your inventory can make an annual chore that people dread into a task that can be completed in seconds. And if something’s easy to do, chances are, it will get done.
Location Decisions
Will you want to know where the most frequently accessed items are located? Will you want to know the locations of your most valuable stock? Lots of small businesses set up their storage locations by feel or sometimes by habit. Once you get in the practice of accurately performing inventory counts, you’ll be able to make better decisions on the best locations for your stock. For tips on naming inventory locations, see: How to Name Inventory Locations.
What Are You Going to Count?
Why you’re tracking inventory should lead directly to what you’re going to count. It may seem overly simplistic or obvious to have to specify what is going to be counted, but if you put a little thought into this, it will help deal with questions that are bound to arise during a count. Even a sole proprietor will be helped by making these decisions in advance because you want to spend as little time as possible thinking during inventory counts and maximize the time spent counting. Also, anyone helping with the count will need to know what to count. Here are a few common categories to help inspire you.
Saleable Items
Anything that may be sold to a customer, this is by far the most popular category of item.
Maintenance Items
Many larger companies use Clearly Inventory to track maintenance items. They find that it’s easier to use a simple web-based application instead of trying to use their complex internal systems.
Raw Materials
Clearly Inventory’s “Bill of Materials” function makes it easy to automatically deduct raw materials when making a finished good. If you track raw materials, you’ll be able to take advantage of this feature.
Furniture, Fixtures, & Equipment
Because it’s so easy to segment your inventory in Clearly Inventory, many companies decide to use the application to track their hard assets as well. This can be a valuable record in the event of a disaster, for accounting purposes, and to monitor damage, theft, or usage.
Rental and/or Movable Equipment
The “Move” function in Clearly Inventory makes it easy to track the movement of items across lots of locations, including temporary locations like events, construction sites, or other field operations.
Cars, Trucks, Vans, Containers, etc.
It’s not uncommon for larger operations to have many vehicles, and given enough time and personnel turnover, some companies even forget how many vehicles they have or where they are. So consider tracking these items in Clearly Inventory as well.
Where Are You Performing Inventory Counts?
Some operations have only one or two locations, while others have thousands. But even the smallest operation may benefit from this checklist of locations where items may exist that need to be counted.
Inventory Counts by Physical Areas
It’s not necessary that you count everything in your entire facility at once, so you may wish to break down your counting activity by physical area. Make sure everyone knows which areas will be counted in advance.
Items That Are “In Transit”
Don’t forget to count items that are out for third-party operations or services, items on loan, or assets held by vendors such as tooling.
Company Agents, Sales Reps, Maintenance Vehicles, etc.
Lots of organizations have inventory that’s kept in a mobile location like a service truck or sales rep’s car. Will you be counting these items? If so, you’ll need to notify the responsible parties of what to count, how, and when to count it.
Items Held by Third Parties
Don’t forget to count items that are out for third-party operations or services, items on loan, or assets held by vendors such as tooling.
Job Sites, Events, Customer Sites, or Other External Locations
Don’t forget remote locations that may not be easy or convenient to count and may require coordination with people on site.
When Are You Performing Inventory Counts?
It’s very difficult to perform counts during operating hours, and you hope to get an accurate count, so try to plan your count during off hours if possible. Also, make sure that everyone involved with the count knows when the count will occur, especially those people who are not on site.
Come up with an estimate of how long it will take to count your stock. Knowing a ballpark figure of how many hours it will take will help you determine how many people will be needed in order to finish the count in the actual amount of time you have available. To get a good estimate, perform a practice count of a fraction of your stock and then multiply that time by the remaining areas to be counted. This will give you the total “person hours” required to count all of your stock. Divide this number by the amount of time available, and you’ll have the number of people necessary to meet the deadline. Finally, add one person to this number to account for the drag in efficiency of having to manage as well as count.